BUSINESS
適正在庫の特徴と計算方法まとめ!実践のポイントは?

目次
在庫管理は企業経営の要となる重要な業務ですが、「適正在庫」の考え方を理解し実践することで、無駄な在庫を持たずコストを削減しながら、必要な商品を必要な時に提供できる体制を整えることができます。本記事では、適正在庫の基本的な考え方から具体的な計算方法、さらには実務での運用方法まで、体系的に解説します。
特に、発注点管理やリードタイムの把握、需要予測など、現場で即実践できるポイントを詳しく説明。トヨタ生産方式に代表される日本の製造業で培われてきた在庫管理のノウハウを活かしながら、中小企業でも取り入れやすい手法を紹介。在庫管理の効率化を目指す経営者や現場担当者の方々に、すぐに役立つ情報をお届けします。
1. 適正在庫とは?安全在庫との違いは?
適正在庫とは、企業が抱える在庫の中で、欠品を防ぎながらも過剰在庫を抑制するために必要最小限の在庫量を指します。適正在庫を維持することで、商品の欠品による機会損失を防ぎつつ、過剰在庫による保管コストの増加や資金の固定化を防ぐことができます。
1.1 適正在庫は最小限の在庫のこと
適正在庫は、企業活動において必要最小限の在庫量を維持することを意味します。過剰な在庫を持つことは保管コストの増加や商品の劣化リスク、キャッシュフローの悪化につながり、逆に在庫不足は販売機会の損失や顧客満足度の低下を招きます。
過剰在庫の問題 | 在庫不足の問題 |
---|---|
保管コストの増加 | 販売機会の損失 |
商品劣化リスク | 顧客満足度低下 |
資金繰りの悪化 | 緊急調達コスト増加 |
1.2 適正在庫を意識するメリット
適正在庫を維持することで、以下のようなメリットが得られます。
1. コスト削減効果
・保管費用の最適化
・在庫管理コストの低減
・商品劣化ロスの防止
2. 経営効率の向上
・在庫回転率の改善
・キャッシュフローの改善
・利益率の向上
3. 顧客満足度の維持
・欠品による機会損失の防止
・安定した商品供給の実現
1.3 安全在庫との違いは?
適正在庫と安全在庫は、以下のような違いがあります。
項目 | 適正在庫 | 安全在庫 |
---|---|---|
目的 | 在庫の最適化 | 欠品防止 |
設定方法 | 上限値と下限値を設定 | 下限値のみ設定 |
管理の焦点 | 過不足のない在庫維持 | 不足リスクへの対応 |
安全在庫は予期せぬ需要増加や納期遅延に備えるための在庫であり、適正在庫は経営効率を考慮した最適な在庫水準を目指すものです。そのため、適正在庫の設定には、より総合的な視点が必要となります。
NECの解説によると、適正在庫の管理には、定期的に発注し、過不足なく在庫を補充することが欠かせないとしています。
2. 計算前に知っておきたい「リードタイム」
適正在庫の計算において、リードタイムを正確に把握することは非常に重要です。リードタイムを適切に把握することで、無駄な在庫を持たず、かつ欠品も防ぐことができるようになります。
2.1 発注リードタイム
発注リードタイムとは、商品の発注から入荷されるまでの期間を指します。発注リードタイムには、注文処理時間、製造時間、輸送時間などが含まれ、これらの要素を正確に把握することが適正在庫の維持に重要です。
要素 | 内容 |
---|---|
注文処理時間 | 発注から取引先での受注処理完了まで |
製造時間 | 製品の生産に要する時間 |
輸送時間 | 配送センターから自社倉庫までの配送期間 |
2.2 製造リードタイム
製造リードタイムは、生産開始から完成までにかかる時間を指します。製造業において、この時間を正確に把握し短縮することは、在庫の適正化に直接的な影響を与えます。
一般的な製造リードタイムの構成要素は以下の通りです。
工程 | 詳細 |
---|---|
段取り時間 | 生産準備に必要な時間 |
加工時間 | 実際の製造に要する時間 |
検査時間 | 品質検査に必要な時間 |
2.3 出荷リードタイム
出荷リードタイムは、商品の出荷指示から顧客への到着までの期間を指します。適切な出荷リードタイムの管理は、顧客満足度の維持と物流コストの最適化に大きく貢献します。
段階 | 所要時間の目安 |
---|---|
ピッキング作業 | 数十分〜数時間 |
梱包作業 | 数十分〜数時間 |
配送時間 | 数時間〜数日 |
NECによると、物流コストとリードタイムがトレードオフの関係となっているため注意が必要です。
これらのリードタイムを正確に把握し、継続的にモニタリングすることで、より精度の高い適正在庫の計算が可能になります。また、各リードタイムの短縮に取り組むことで、在庫回転率の向上にもつながります。
3. 適正在庫で使う計算式と計算方法
適正在庫の計算にはいくつかのアプローチ方法があります。ここでは主要な3つの計算方法について詳しく解説します。
3.1 実務から見る基本的な計算方法
実務における最も基本的な適正在庫の計算式は以下の通りです。
項目 | 計算式 |
---|---|
適正在庫量 | 安全在庫量 + サイクル在庫量 |
安全在庫量 | リードタイム中の平均需要量 × 安全係数 |
サイクル在庫量 | 1回あたりの発注量 ÷ 2 |
安全在庫量は、予期せぬ需要増加や納品遅延などのリスクに備えるための在庫量です。安全係数は企業によって設定が異なりますが、一般的に1.2〜1.5の範囲で設定されることが多いです。
3.2 経営から見る「在庫回転率」による計算方法
経営的視点からは、在庫回転率を用いた計算方法が重要です。
指標 | 計算式 |
---|---|
在庫回転率 | 年間売上高 ÷ 平均在庫金額 |
適正在庫金額 | 月間売上高 × (1 ÷ 目標在庫回転率) × 12 |
在庫回転率が高いほど在庫効率が良く、一般的に製造業では12回転(1ヶ月で1回転)程度が目安とされています。業界や企業規模によって適正な回転率は異なります。
3.3 「交叉比率」での計算方法
交叉比率は、在庫の収益性を評価する指標として用いられます。
指標 | 計算式 |
---|---|
交叉比率 | 在庫回転率 × 粗利益率 |
適正在庫金額 | 目標売上高 ÷ 目標交叉比率 |
交叉比率が高いほど在庫効率と収益性の両面で優れていることを示し、一般的に100%以上が望ましいとされています。
東芝テックの記事によると、交差比率が高いほど儲けを生み出している商品となり、例えばディスカウントショップや激安スーパーは薄利多売の商品を中心とした収益構造では在庫回転率を上げる必要があります。
4. 適正在庫の計算をする際に気を付けるべきこと
適正在庫の計算を行う際には、いくつかの重要な注意点があります。単に数式に当てはめるだけでなく、実務的な視点を持って計算することが重要です。ここでは、適正在庫を計算する上で押さえておくべきポイントを解説します。
4.1 平均在庫は長いスパンで計算する
適正在庫を計算する際の大きな注意点として、平均在庫の算出期間があります。短期間のデータのみで平均在庫を計算すると、季節変動や特殊要因による影響を受けやすく、適切な数値が得られない可能性があります。
算出期間 | 特徴 | 注意点 |
---|---|---|
1ヶ月 | 最新の傾向を反映 | 一時的な変動の影響を受けやすい |
3ヶ月 | 季節要因を含む | 中期的な変動は捉えられる |
1年以上 | 長期的な傾向を把握 | 最適な算出期間とされる |
NECでは、適正在庫の算出には出荷データの蓄積が必要不可欠としています。
4.2 適正在庫の最適化を続ける
適正在庫は一度計算して終わりではありません。市場環境や需要の変化、自社の経営方針の変更などに応じて、定期的な見直しと最適化が必要です。以下のタイミングで見直しを行うことが推奨されます。
- 四半期ごとの業績評価時
- 新商品の投入時
- 競合他社の動向に変化があった時
- 経営方針の変更時
- リードタイムに変更があった時
中小企業庁によると、適正在庫を保つことで安定的な売り上げにつながるとしています。
見直し頻度 | メリット | デメリット |
---|---|---|
毎月 | 変化への即時対応が可能 | 作業負担が大きい |
四半期 | バランスの取れた見直し | 一定の作業負担 |
半年・年次 | 作業負担が少ない | 変化への対応が遅れる |
これらの点に注意を払いながら適正在庫の計算を行うことで、より精度の高い在庫管理が可能になります。重要なのは、自社の状況に合わせて柔軟に計算方法を調整し、継続的な改善を行っていく姿勢です。
5. 適正在庫を保つためのポイント
適正在庫の維持は企業の収益に直結する重要な課題です。ここでは、適正在庫を効果的に保つための具体的なポイントを解説します。
5.1 全社視点で適正在庫を考える
適正在庫の管理には、部門を超えた全社的な取り組みが不可欠です。
各部門で適正在庫に対する考え方が異なると、在庫の過不足が生じやすくなります。例えば、営業部門は販売機会損失を避けるため多めの在庫を望む一方、製造部門は生産効率を重視して最小限の在庫を目指すといった具合です。
部門 | 在庫に対する考え方 | 重視するポイント |
---|---|---|
営業部門 | 余裕を持った在庫 | 販売機会の確保 |
製造部門 | 最小限の在庫 | 生産効率の向上 |
物流部門 | 効率的な在庫 | 保管・配送コスト |
5.2 発注点の管理をする
適正在庫を維持するには、適切な発注点の設定と管理が重要です。
発注点とは、在庫が一定水準まで減少した時点で追加発注を行うための基準となる在庫量のことです。この発注点を適切に設定することで、過剰在庫や在庫切れを防ぐことができます。
発注方式 | 特徴 | メリット | デメリット |
---|---|---|---|
定期発注方式 | 一定期間ごとに発注 | 発注業務の計画が立てやすい | 在庫変動に柔軟に対応できない |
定量発注方式 | 発注点に達したら発注 | 在庫の変動に対応しやすい | 発注業務の負担が大きい |
5.3 調達や製造のリードタイムを短縮する
リードタイムの短縮は適正在庫維持の重要な要素です。
リードタイムが長いほど必要な在庫量は増加し、在庫管理のコストも上昇します。このため以下の取り組みが重要です。
- サプライヤーとの関係強化による調達リードタイムの短縮
- 生産工程の効率化による製造リードタイムの短縮
- 物流システムの改善による配送リードタイムの短縮
5.4 需要の予測をしておく
精度の高い需要予測は、適正在庫維持の基盤となります。
需要予測の精度を上げることで、発注量や生産量を適切に調整し、在庫の最適化が可能になります。需要予測には以下のような方法があります。
- 過去の販売データ分析による予測
- 市場動向や経済指標の活用
- AIを活用した高度な需要予測
- 顧客からの発注予定情報の活用
経済産業省によると、需要予測の精度向上により在庫コストを削減できるとされています。
企業の規模や業態に関わらず、これらのポイントを意識した取り組みを継続的に行うことで、適正在庫の維持が可能となります。
6. 手軽で適切な在庫管理ならUMWELT!
在庫管理を効率的に行うために、在庫管理システムの導入は非常に有効な手段です。しかし、従来型の在庫管理システムには、以下のような課題があります。
課題 | 詳細 |
---|---|
導入コストが高い | 初期費用やランニングコストが大きな負担に |
専門知識が必要 | プログラミングやネットワークの知識が求められる |
既存システムとの連携が困難 | システム改修に多大な工数がかかる |
6.1 UMWELTの特長
適正在庫は、定期的に最適化の見直しを続ける必要があり、手間と時間がかかります。手軽に適正在庫の維持を実現したいと考えているならば、在庫管理システムの導入も検討してみると良いでしょう。在庫管理システムを導入することにより、在庫が入荷されてから出荷されるまでの位置情報、入出荷日時・賞味期限といった在庫情報を適切に管理できます。
しかし、在庫管理システムの導入には、ネットワークやプログラミング、システムを管理できる知識や技能が求められます。そこでネットワークやプログラミングの知識がなくても在庫管理システムを利用したいと考えている方にオススメなのが、TRYETINGが提供するノーコードツール「UMWELT」というサービスです。
UMWELTには常時100種類ものアルゴリズムが搭載されており、それらをレゴブロックのように自由に組み合わせることで、誰でも簡単に求めているシステム構築が可能です。また、UMWELTはAPIを介して接続する特性上、既存システムに手を加えずに利用できるため、煩わしい社内調整のコストも最小限です。
UMWELTは、ネットワークやプログラミングの知識がない方でも、簡単に在庫管理システムの導入、構築、作業、管理が行えます。さらに導入後はコンサルサポートも利用できるため、困った時も安心です。
6.2 導入効果
実際の導入事例では、以下のような効果が報告されています:
- 在庫回転率の向上
- 欠品率の低下
- 在庫管理業務の工数削減
システム導入をご検討の方は、UMWELTの詳細ページから、より詳しい情報をご確認いただけます。
7. まとめ
適正在庫は、経営効率と顧客満足の両立に欠かせない重要な要素です。計算方法は、リードタイムを考慮した基本的な計算、在庫回転率による方法、交叉比率による方法など、目的に応じて使い分けることが重要です。
効果的な適正在庫管理のためには、全社的な視点での取り組み、発注点の適切な設定、リードタイムの短縮、そして需要予測の精度向上が必要不可欠となります。特に製造業や小売業においては、季節変動や市場トレンドも考慮に入れた柔軟な在庫管理が求められます。
また、在庫管理システムの導入により、人的ミスを減らし、より正確な在庫管理を実現することができます。適正在庫の実現は一朝一夕にはいきませんが、継続的な改善と最適化により、コスト削減と業務効率化を両立することが可能です。
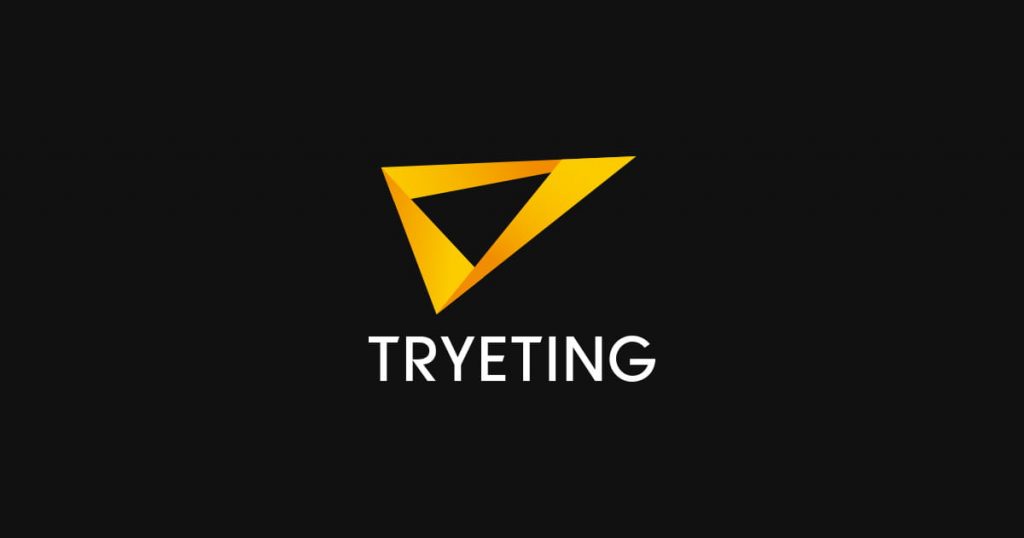
TRYETING
公式
TRYETING公式です。
お知らせやIR情報などを発信します。